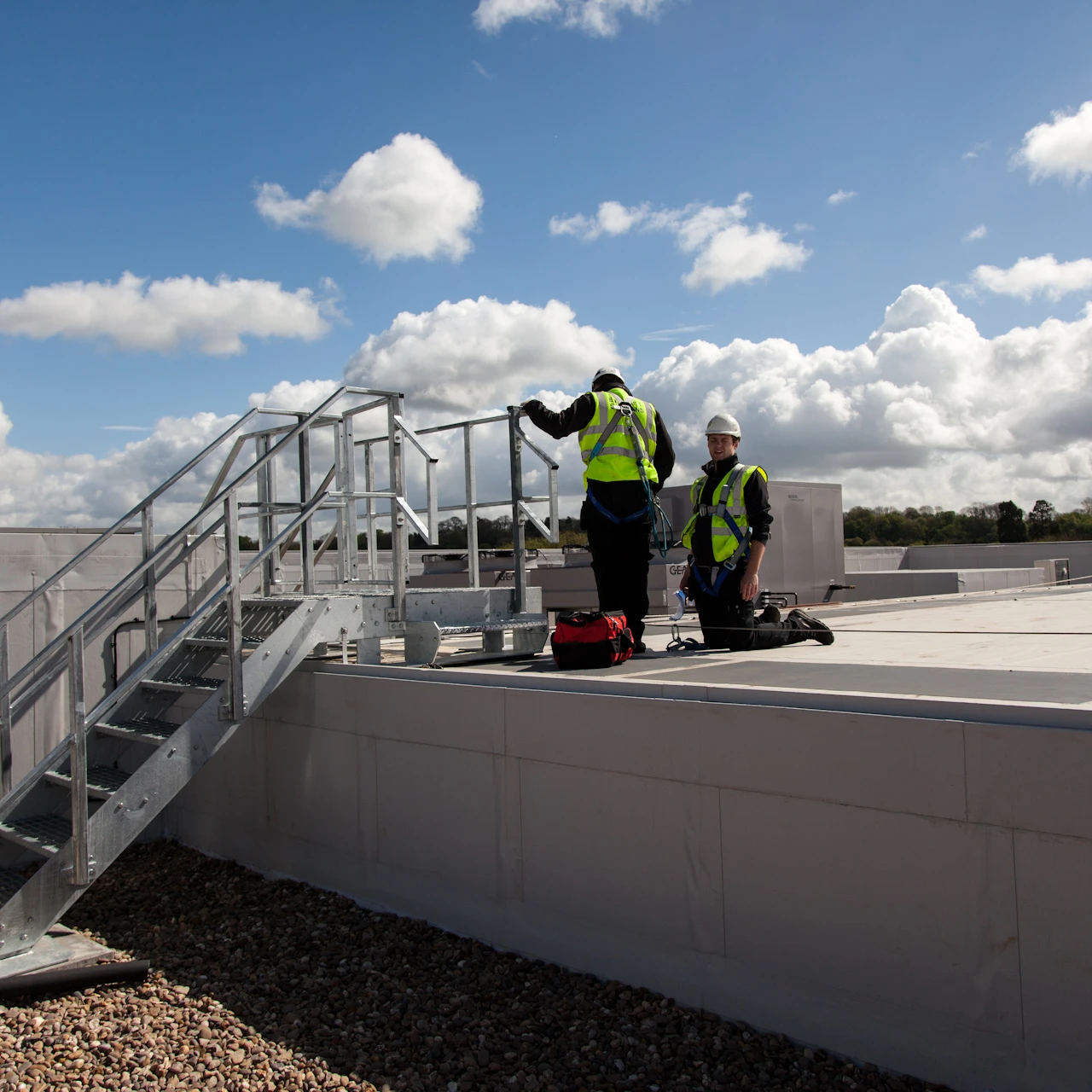
- Knowledge Base
- Blog
- Fall protection testing and inspection: What are your business responsibilities?
Fall protection testing and inspection: What are your business responsibilities?
Implementing tests & inspections of your height safety equipment is vital and knowing your requirements could save your company time & money, as well as reduce any potential risks. We’re examining the responsibilities and duties for businesses, as well as the current legislation in place for a multitude of protection equipment from ladders to mansafe systems.
Fall Protection, Eyebolt Test & Inspection
Nearly every building needs some form of fall protection whether it’s for window cleaning, gutter & plant maintenance, or access between levels.
With numerous forms of fall protection available, it’s important to identify which fall protection you require. As with any form of protection, it is the duty holder’s responsibility to ensure that, prior to use, the equipment provided is inspected by a competent person. The Working at Height Regulations (WAHR) 2005 states ‘Every employer shall ensure that, where the safety of work equipment depends on how it is installed or assembled, it is not used after installation or assembly in any position unless it has been inspected in that position.’
Cable-based systems, rail-based systems & single-point anchors are all forms of fall protection; which should be inspected at least every 12 months. It is also stated in the WAHR; ‘Where work is carried out at height, every employer shall take suitable and sufficient measures to prevent, so far as is reasonably practicable, any person falling a distance liable to cause personal injury which is why it is so important that all testing, inspection, and certification of fall protection systems are carried out in accordance with current British Standards; BS EN 795 & BS EN 7883.
Handrail, Guardrail Balustrade & Barrier Inspection
Although handrails & barriers are one of the simplest forms of protection equipment, they still require regular maintenance & inspections like any other form of protection. The Working at Height Regulations (WAHR) 2005 & The Provision and Use of Work Equipment Regulations (PUWER) 1998 both state that such equipment should be inspected & maintained by a competent person; manufacturers suggest this should be a frequency not exceeding 12 months.
The Provision and Use of Work Equipment Regulations (PUWER) 1998 states that the ‘duty holder’ must ensure that any work equipment provided is ‘Suitable for use, and for the purpose and conditions in which it is used. Maintained in a safe condition for use so that people’s Health and Safety are not at risk, and Inspected in certain circumstances to ensure that it is and continues to be safe for use.’
The duty holder is responsible for ensuring that all the expected checks are followed through; this is the person who has, to any extent, control of premises; in plain English, this means it could be the person in charge of health & safety, a manager or a landlord. It’s vital that everyone knows who the duty holder is to ensure everything is kept compliant with relevant standards such as BS EN 795. Regular inspections are critical because they provide peace of mind and help reduce the risks to workers.
Ladders, Steps, Walkways & Access Equipment Inspection
Equipment such as ladders, steps, walkways & access equipment has often been installed for planned maintenance purposes. Regular test & inspection is required for all of the above as they fall under the (PUWER) 1998.
Fixed ladder Inspection
Fixed ladders are usually formed from steel or aluminum and are put in place to provide access to places of work (internally or externally). It is vital that they are inspected to ensure the safety of workers, regardless of their location and whether they provide access to rooftops, plants or silos.
Inspections ensure that installations are still compliant with current legislation as well as checking for damage, corrosion, or loose fittings. They will also check for items that may present an obvious hazard such as slips, trips, falls, or impact damage. As part of any ladder inspection, the fixings are checked to ensure they remain secure; if there are self-closing gates at the head of the ladder these should also be inspected to ensure.
Fixed ladders will need to be inspected at least every 12 months. The duty holder should know how often the tests need to be carried out as they will be held responsible if safety precautions have not been followed out to a high enough standard. Ladder inspections should always be accompanied by a report of any issues that were discovered and what rectifying measures have been put in place to make the equipment safe to use; it is the duty holder’s responsibility to keep hold of this report & refer back to when required, in order to keep up with regular tests & inspections. After each inspection Eurosafe Solutions will tag a unique reference number & provide a detailed report stating the date of inspection and any findings.
All of the following British standards apply to fixed ladders:
BS 4211:2005+A1:2008 – Specification for permanently fixed ladders.
BS 5395-3:1985 – Code of Practice for the design of industrial-type stairs, permanent ladders, and walkways.
BS EN 14122 – Safety of machinery. Permanent means of access to machinery. Working platforms and walkways.
Temporary ladder Inspection
Temporary ladders are put in place for short duration tasks (30 minutes or less) which is why a risk assessment must be done prior to deciding whether a temporary ladder is suitable or whether a more suitable form of access could be used. There are many regulations that are applicable to temporary ladders, with (PUWER) 1998 & The Working at Height Regulations (WAHR) 2005 generally considered the most applicable.
In the WAHR it is stated that ladders must be tested & maintained annually or more frequently depending on use; it also states that work equipment should be inspected ‘each time that exceptional circumstances which are liable to jeopardise the safety of the work equipment have occurred. The duty holder should be aware that inspections are required every 12 months (minimum) to avoid the risk of people being injured.
All of the following British standards apply to temporary ladders:
BS 1129 Specification for portable timber ladders, steps, trestles, and lightweight stagings
BS 2037 Specification for portable aluminum ladders, steps, trestles, and lightweight stagings
BS EN 131 Ladders (Specification for terms, types, functional sizes; Specification for requirements, testing, marking; User instructions; Single or multiple hinge-joint ladders)
Ladder ties
Ladder restraint ties are typically installed discreetly adjacent to or beneath windows on the outside of buildings. When used in conjunction with a ratchet strap to restrain the ladder they provide a safe means of securing a ladder for short duration tasks such as window cleaning; making them a perfect addition to temporary ladders to maximise safety. As such a critical part of worker safety, this equipment is covered under 1998 (PUWER) and BS EN 8539.
Ladder ties require a regular visual inspection, combined with a physical pull test to determine the suitability of the fixing; avoiding these inspections ladder ties are put under a lot of tension due to the restraint strap; if not tested correctly it could pull out after the operator has ascended the ladder leading to unthinkable consequences. To stay compliant the duty holder should ensure all ladder ties are tested every 12 months (minimum).
Façade Access Test & Inspection
Facades are usually an aesthetically pleasing element to the building but they also have an effect on the building’s efficiency. Due to their location (at the front point of the building over the entrance) a lot of equipment must be in place to make them accessible. Some of the equipment in place for facades include abseil rails, abseil anchors & cradles. The duty holder is responsible to ensure that all tests and inspections of height safety equipment are followed to the correct standards & regulations. Abseil rails and abseil anchors both fall under LOLER and must be tested every 6 months. Cradles must be tested every 3 months under LOLER & BS6037.
All of the following regulations apply to façade access:
BS EN 795 – Personal fall protection equipment. Anchor devices
BS 7883 2005 – Code of practice for the design, selection, installation, use, and maintenance of anchor devices conforming to BS EN 795
LOLER 1998 – Lifting Operations and Lifting Equipment Regulations
BS6037 – Code of practice for the planning, design, installation, and use of permanently installed access equipment
PUWER 1998 – Provision and Use of Work Equipment Regulations
Additional Test & Inspection Services
Brise soleil is typically put in place to reduce air conditioning & heating costs by retaining heat & sunlight during the winter months whilst lowering heat gain during the summer months. The system can provide great advantages for businesses & organisations however without proper inspection it could lead to injuries just like any other form of protection. It is a requirement that the inspection works are carried out regularly to prevent wear & tear, therefore, minimising potential injury. Brise Soleils come under the Provision and Use of Work Equipment Regulations 1998 (PUWER). The duty holder should ensure inspections are carried out at least every 12 months in accordance with manufacturers guidance. When an inspection is carried out they will check the fixings of external architecture as well as check for divergence, vibration, or fluctuations in the system which could potentially cause fatigue or cracking.
As with any form of protection, it is the duty holder’s responsibility to ensure that lightning protection systems are regularly checked and maintained. Inspections to lightning protection include undertaking an earth resistance test using calibrated test meters in addition to visually checking the down conductors that are affixed to the wall for signs of damage or missing components, but most importantly the ‘airstrike’ components should be thoroughly inspected because these are the parts of the system which are most likely to be struck by lightning as they’re located on the roof. Not only do inspections minimise risks but it’s also a requirement under the Electricity at Work Regulations – Reg 4 part 2:1989 to have lightning protection systems professionally maintained. The duty holder is responsible for ensuring lightning protection inspections are followed every 12 months (minimum) to ensure continuity.
Every building should have a fire extinguisher in place because they’re a critical part of any building’s fire and rescue plan. It’s extremely important that the fire extinguishers are regularly tested to ensure that they work correctly; this way they will be available and working in the event of an emergency. It’s essential this is done every 12 months to ensure safety; it’s also a requirement under the British Standard BS 5306 (parts 3 & 8). The last thing any company or person wants to find out in the event of a fire is that the extinguisher doesn’t work; this is why it is vital that the duty holder ensures these checks are done regularly.
It’s not majorly common that a building will have a flagpole in place however there are quite a few town halls, city halls, stately homes & other high-profile buildings which might have one (or more) in place. It’s vital that flagpoles are inspected & are compliant with the relevant regulations in order to minimise public liability & ensure safety. The current regulations for flagpoles fall within the parameters of the LOLER 1998 regulations (the raising and lowering of materials) which also covers associated wires, shackles, hooks, pole carriers, and slings; all of which should be inspected at least every 12 months. Although it can sometimes be difficult to understand how a flagpole can be a danger, it should not be underestimated; the force of the wind on the fabric of the flag and the pole itself can be quite considerable which is why safety checks are so important. During inspections, the engineers will test the flag, pole, halyard, pulleys, and holding down bolts, with both a function check and a thorough visual inspection. The duty holder is responsible to acknowledge the regulations put in place and ensure inspections are followed in accordance with LOLER.
Blocked gutters can cause major problems to a building; especially if left for too long because this can lead to water damage; creating major disruption and costly expenses due to unavoidable repairs. In order to reduce these risks & save on maintenance costs, regular gutter cleaning should be implemented. HSE Guidance suggests that the duty holder should ‘avoid work at height where they can and ‘use work equipment or other measures to prevent falls where they cannot avoid working at height’. If this cannot be avoided then only competent people with a safe system of work should undertake tasks such as window cleaning or gutter cleaning.
It’s common knowledge that the purpose of PPE (personal protective equipment) is to keep workers safe and protected however in order to serve their purpose they must be regularly checked. Common issues with PPE can be general wear and tear, misuse, and exposure to dirt, grit, UV light, or chemicals.; all of which can lead to damaged PPE that has lost its effectiveness. The Work at Height Safety Association (WAHSA) technical guidance brings together the recommendations of the PPE regs 1992, BS EN 365:2004, and BS 8347:2005 CoP, HSE Guideline INDG 367. In order to stay compliant it’s critical that employers establish an inspection regime, which should be drawn up by a competent person and followed out as required. The inspection regime should be specific to the site and should consider the frequency of use and the type of PPE provided. The WAHSA technical note advocates that this regime should include inspection of equipment (including unique identification), the frequency & type of inspection (pre-use checks, detailed, interim inspection), actions to be taken, records of the inspections, as well as trained users & a designated competent person to ensure inspections are carried out. Detailed inspections are expected to be followed out every 12 months as a minimum legal requirement under BS EN 365:2004. However, the recommended guidance under BS 8437: 2005 & INDG367 suggests that inspection intervals do not exceed 6 months or 3 months when used in arduous conditions such as demolition, steel erection, scaffolding, steel masts, or towers with sharp edges.
Wind turbines are typically located in exposed and often remote areas which is why it’s so vital that any fall protection included is thoroughly inspected. Some of the equipment which can be found on wind turbines include fixed access ladders, anchor points for PPE, rescue equipment, goods hoists & fire extinguishers. Each aspect of fall protection should be looked at as an individual piece of equipment and the duty holder should ensure that inspections are followed out with relevant standards to be compliant. For more information on the regulations in place, please click any of the links above.
The typical use of Rail and Beams is to raise and lower goods; used in many buildings throughout the UK with one of the most common examples being warehouses where they are used to lift & lower items to a lorry from the warehouse entrance.
The main purpose of the lifting equipment will determine how often it needs to be tested to be compliant with LOLER (Lifting Operations and Lifting Equipment Regulations) 1998 regulations. If the equipment is being used to lift people or is an accessory for lifting it will need to be inspected every 6 months (minimum) whereas any other lifting equipment can be inspected every 12 months (minimum) except for exceptional circumstances. Any circumstance which could jeopardise the safety of the equipment will create cause for another inspection. The duty holder should always be aware of how often these inspections need to be carried out as it is their responsibility. Most beams will already have a testing procedure in place which can be established from the Safe Working Load (SWL) sticker. In situations where the documentation is not available it’s important that the procedure & testing requirements are determined to avoid safety risks that could have horrific consequences if such a beam failed.
Anchor points are permanently fixed into the structure of the building and are generally used for the suspension of decorations and signage such as Christmas decorations or banners. As harmless as decorations might seem, the chance of one falling could cause numerous accidents and injuries which is why it is so important they are inspected every 12 months (minimum). LOLER 1998 regulations and British Standards BS 8539 & BS 7883 state that inspections must be followed out at 12-month intervals & include a load test to stay compliant. A load test is when the anchor points are physically tested to ensure that they’re still capable of suspending the required load.
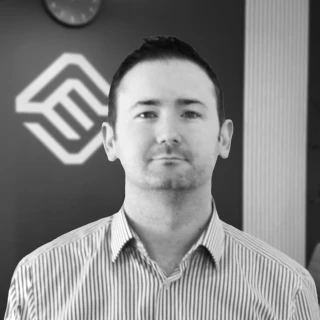